Fundamentals of Fluid Power (Hydraulic Systems)
Offered by The University of Minnesota
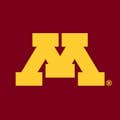
The University of Minnesota is among the largest public research universities in the country, offering undergraduate, graduate, and professional students a multitude of opportunities for study and research. Located at the heart of one of the nation’s most vibrant, diverse metropolitan communities, students on the campuses in Minneapolis and St. Paul benefit from extensive partnerships with world-renowned health centers, international corporations, government agencies, and arts, nonprofit, and public service organizations.
About this Course
Fluid power has the highest power density of all conventional power-transmission technologies. Learn the benefits and limitations of fluid power, how to analyze fluid power components and circuits, and how to design and simulate fluid power circuits for applications.
In this course, you will be introduced to the fundamental principles and analytical modeling of fluid power components, circuits, and systems. You will learn the benefits and limitations of fluid power compared with other power transmission technologies; the operation, use, and symbols of common hydraulic components; how to formulate and analyze models of hydraulic components and circuits; and how to design and predict the performance of fluid power circuits. This course is supported by the National Science Foundation Engineering Research Center for Compact and Efficient Fluid Power, and is endorsed by the National Fluid Power Association, the leading industry trade group in fluid power.
Instructors
1. James D. Van De Ven, PhD
Assistant Professor
Mechanical Engineering
University of Minnesota
James D. Van de Ven is an assistant professor at the University of Minnesota in the Department of Mechanical Engineering where he operates the Mechanical Energy and Power Systems (MEPS) Laboratory. Professor Van de Ven received his Ph.D. in Mechanical Engineering from the University of Minnesota in 2006. From 2007 to 2011, he was an assistant professor in the Mechanical Engineering Department at Worcester Polytechnic Institute. Prior to joining WPI, Dr. Van de Ven was a post-doctoral research associate at the University of Minnesota in the National Science Foundation-sponsored Engineering Research Center for Compact and Efficient Fluid Power. Dr. Van de Ven’s research interests are in efficient energy conversion, energy storage, fluid power, kinematics, and machine design.
2. Will Durfee, PhD
Morse Alumni Distinguished Teaching Professor
Mechanical Engineering
University of Minnesota
Will Durfee is professor and director of Design Education in the Department of Mechanical Engineering at the University of Minnesota, Minneapolis, USA. He received the A.B. degree in engineering and applied physics from Harvard University and the M.S. and Ph.D. degrees in Mechanical Engineering from the Massachusetts Institute of Technology. His professional interests include the design of medical devices, rehabilitation engineering, advanced orthotics, biomechanics and physiology of human muscle including electrical stimulation of muscle, product design, and design education.
Syllabus – What you will learn from this course
Week 1: Fundamentals of Fluid Power.
An overview of the course, introduction to hydraulics and pneumatic, and introduction to fundamental concepts of fluid power through the cylinder.
Week 2: Components and Concepts: Part 1
Circuit diagrams, the written language of fluid power, and how fluid flows through conduits. We hope that you find the hydraulic circuits on the mowing machine as interesting as we did.
Week 3: Components and Concepts: Part 2
This will be a busy week diving into valves and pumps. We will discuss how basic valves function, how to use them in hydraulic circuits, and how to calculate pressure drop for a given flow rate, or vice versa. The videos will directly address the discussion on the forum about seeing hydraulic components working in real world circuits. In our discussion of pumps we will look at many different positive displacement pumps, exploring flow ripple and pump efficiency, look at the supporting components that form a hydraulic power supply, and see how we can make a transmission with a hydraulic pump and a motor. We are now into the heart of this course; we hope you enjoy seeing the components come together into useful circuits.
Week 4: Predicting Performance Through Simulation.
This week is entirely devoted to you learning how to use Simscape Fluids (formerly SimHydraulics), the fluid power simulation application that we use in the course. The lecture provides an introduction to computer-based, object-oriented simulation, and goes through a demo of using Simscape Fluids. The homework assignment contains the real work because this is where you will learn to use Simscape Fluids. The homework ends with an open-ended problem that encourages you to branch out on your own and create and run simulations based on examples listed in the course Simscape Fluids resource page or on any other fluid power system that interests you. We will be monitoring the discussion boards to help you with any technical problems with Simscape Fluids.
*NOTE: The lecture videos were created using an earlier version of SimHydraulics; some small difference exist with the most recent version of Simscape Fluids, but the general approach is the same. *THERE IS NO QUIZ THIS WEEK as we recognize that a few of you may not be able to get Simscape Fluids running on your computer. Happy simulating!
Week 5: Fluid Properties.
This week we will take a dive into hydraulic fluids (no pun intended) and how their properties and behavior influence the circuit operation. In the lectures, you will see the water hammer effect and explore the assumption of fluid incompressibility. We encourage you to use your new knowledge of fluid behavior and simulation to create virtual experiments that explore how fluid properties influence the behavior of a circuit. Share your observations on the discussion forum.
Week 6: Advanced Components and Systems and Course Summary.
This week you will learn about two new components, the accumulator, which stores hydraulic energy, and the servo valve, which provides fast and precise flow control. We will then be pulling together topics from throughout the course to look at servo hydraulic systems and hydraulic hybrid vehicles. You will get a chance to use simulation to explore how these advanced systems function and how the behavior of individual components influences the system operation.
You can share your Course Certificates in the Certifications section of your LinkedIn profile, on printed resumes, CVs, or other documents.
To register, click on Enroll now
Abdo
[email protected]